ERW Pipes
ERW stands for electric resistant weld. A few advantages to note with ERW pipes. First one is its cost effective as compare to structural steel base products. It’s stronger when load strength is compared with other structure base products because there is no fusion metal used during the manufacturing process. This means that the pipe is extremely strong and durable. Its lighter then few others structural steel products because it is light & it’s easy to use as compare to other structural products. It’s easily available in local markets too.When there is no fusion metal used during the manufacturing process the weld seam cannot be seen or felt. This is a major difference when looking at the double submerged arc welding process, which creates an obvious welded bead that might need to be eliminated. With the advances in high-frequency electric currents for welding, the process is far easier and safer.
MANUFACTURING PROCESS OF ERW PIPES:
- DECOILING & STRAIGHTNING: Incoming coils are peeled and unwrapped for presentation into the rolls. Rolls remove the coil set to produce a flat steel strip.
- JOINING OF TWO COILS PROCESS: Coil ends are joined together with a butt weld to produce a continuous flat steel strip.
- TRIMMING OF EDGES: Slitter blades and edge milling trims strip edges to provide the precise strip width required during the forming and ERW seam welding process.
- FORMATION OF PIPES : The forming process begins at the breakdown pass where the material is gradually starts getting bend from a flat steel strip into a rounded tube for presentation to the ERW seam welder.
- Electric Resistant Weld(ERW) Welding: A high frequency electrical current flows through contact tips into the strip edges to produce the heat required for bonding the strip edges together as the material passes through the weld roll stand.
- Quality Check Parameters: Once the welding is complete, the finished pipe is visually inspected by quality control chemist (QCC) to ensure the weld is defect-free.
TECHNICAL DATA FOR ERW PIPES
MECHANICAL PROPERTIES | |||
GRADES | YIELD STRESS
(MINIMUM) |
TENSILE STRENGTH
(MINIMUM) |
ELONGATION %
(MINIMUM) |
YST 210 | 210 | 330 | 20 |
YST 240 | 240 | 410 | 17 |
YST 310 | 310 | 450 | 14 |
YST 355 | 355 | 490 | 10 |
- FOR TUBE SIZE UPTO AND INCLUDING 25MM NB, ELONGATION OF 12% SHALL BE PERMISSIBLE.
- FOR CHEMICAL COMPOSITION TAKE REFERENCE FROM IS 10748:2004.
- FOR YST355 [The Indian Standard (5th Revision)was adopted by BIS,approved by the Metallurgical Engineering Division Council.]
- Reference has been derived from the (BS EN 10219-1:2005 cold formed welded structural hollow section,plane ended steel tube welded or seamless).
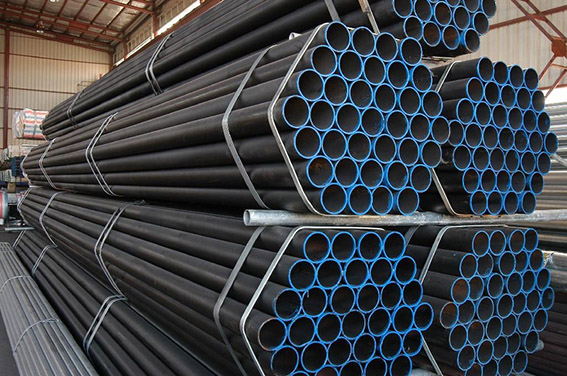